CO₂ Transcritical Refrigeration at Scale: Advancing Industrial Efficiency in Ecuador
CO₂ Transcritical Refrigeration at Scale: Advancing Industrial Efficiency in Ecuador
In the industrial refrigeration landscape, CO₂ transcritical systems are proving to be both a high-efficiency and sustainable alternative to traditional refrigerants. A large-scale shrimp processing facility in Ecuador has adopted this technology, marking a significant step toward reducing environmental impact while maximizing operational performance.
This project integrates a fully CO₂ transcritical refrigeration system with a carefully engineered design to meet the facility’s stringent cooling demands:
- 46 medium-temperature (MT) transcritical compressors (nominal capacity: 1940 HP)
- 33 low-temperature (LT) compressors, ME type (nominal capacity: 1060 HP)
- 6MW of total installed refrigeration capacity, ensuring system stability and redundancy
- 7 operational refrigeration units, each optimized for specific process requirements
- 26 industrial evaporators, distributed strategically to maintain uniform cooling
- 12 gas coolers (each 8x800mm), maximizing heat rejection efficiency
- 2 LT pump stations, each with 3500L vessels, designed for precise liquid distribution
Key Technical Innovations
This CO₂ transcritical system incorporates advanced refrigeration principles that enhance both efficiency and sustainability:
- Mechanical Subcooling: Improves system efficiency by reducing flash gas formation, increasing cooling capacity without additional energy input.
- Vapor Ejectors: Enhance energy efficiency by recovering energy lost during pressure reduction from the gas cooler to the liquid line. This innovative approach reduces compressor workload while consistently meeting cooling demands.
- Hot Gas Defrost: Enhances heat transfer efficiency while minimizing energy consumption and frost buildup within evaporators.
- Heat Recovery Integration: Captures waste heat from the refrigeration cycle to preheat water, reducing overall energy demand.
Performance Metrics
The system is designed to operate at ultra-low and low temperatures, ensuring high thermal stability and energy optimization across different process zones:
- Ultra-LT Evaporation (-45°C/-42°C): 1620 kW capacity
- LT Evaporation (-32°C/-25°C): 1530 kW capacity
- MT Direct Expansion (-5°C/-3°C): 460 kW capacity
- MPG20% Brine System (+1°C): 640 kW capacity
- Air Conditioning Water (+6°C): 1000 kW capacity
- Heat Recovery Water (55°C/65°C): 1300 kW capacity
- Total Gas Cooler Heat Rejection: 8300 kW
Impact on Industrial Refrigeration
This facility represents one of the largest fully CO₂ transcritical refrigeration installations in the region, demonstrating the viability of CO₂ as a long-term solution for large-scale food processing. Compared to conventional HFC-based systems, CO₂ transcritical technology offers:
- Lower Global Warming Potential (GWP = 1), eliminating reliance on high-GWP synthetic refrigerants.
- Higher Thermodynamic Efficiency, especially in low-temperature applications.
- Enhanced Energy Recovery Capabilities, reducing auxiliary heating requirements.
- Improved Safety & Regulatory Compliance, aligning with international F-Gas reduction policies.
A New Standard for Industrial Refrigeration
The scale and complexity of this installation highlight the growing shift toward environmentally responsible and high-performance refrigeration solutions. CO₂ transcritical technology is no longer an emerging trend—it is now a proven, scalable solution that aligns with global efforts to reduce carbon footprints in industrial operations.
The adoption of CO₂ refrigeration in large-scale applications like this sets a precedent for the future of industrial cooling—one that balances performance, sustainability, and energy efficiency.
Building Connections
On LinkedIn
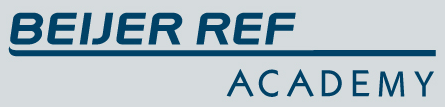
Become a CO² Specialist
Beijer Ref Academy will offer technicians and installers the opportunity to learn how to operate CO2 refrigeration systems in different configurations.