CO2 Refrigeration Systems and the principles of Lean Production
Today, sustainability is becoming more and more important. Industries and companies are constantly seeking ways to reduce their environmental impact. One key concept that has gained attention is Lean Production. Today, we will explore the relationship between this methodology and CO2 Refrigeration Systems.
Lean Production is about making things in a smarter way to reduce waste and maximize efficiency in the production process. It focuses on eliminating activities that don’t add value, optimizing resources, and improving operations.
And where does CO2 Refrigeration come in? It is part of an industry that’s always looking to improve because the need for more eco-friendly technologies is growing. Using Lean Production techniques is an opportunity to reduce costs and make these systems more efficient and better for the planet.
In this article, we step into how Lean Production can make a big difference in the process of producing CO2 refrigeration systems. Seeing, in specific, how it happens inside SCM Frigo. From value stream mapping to reviewing working methods, we explore how Lean principles can revolutionize manufacturing processes in this critical industry.
Introducing Lean Production and its cost and efficiency benefits
This concept is more than a methodology. It is also, and more importantly, a mindset. It’s about always trying to do better and creating more value. This idea started with Toyota and has spread to all sorts of businesses and industries, offering an alternative to how the work is supposed to be done.
At the heart of Lean Production is waste reduction. This means looking closely at how things are made and cutting out steps that don’t add value to the final product. This approach not only enhances efficiency; it also reinforces a culture of empowerment, where frontline workers are motivated to identify and address inefficiencies in real-time. For example, in SCM Frigo “every worker and every working cell has a touch screen monitor. So, we don’t have more paper and all the information runs by digital in each working station”, explains Riccardo Ricci, our Operation Director.
The beginning
Lean Production was introduced in SCM Frigo in 2018 and, since then, the conclusion has been clear: “Now we are working really as a team, focused on what the customer wants”, says Riccardo Ricci. Quality delivery and cost reduction are the foundations. “As a team, we focus on which are the main sources of waste that we have in our production, and we try to find a solution to reduce or cancel that waste. Everyone in the factory works to bring suggestions or to notice some problem in the production line”.
In practice, “every morning, 9 am, everyone involved in the factory, from the managers to the team leaders, meet and discuss how to move the production unit by unit.” A map is placed in the factory with different tickets that represent one unit in specific. It is a visual solution to help follow how the production is developing and what information is available about the products. “We observe, we ask for suggestions, and we take all this information to make the workers’ life easier”.
In the context of CO2 refrigeration systems, value stream mapping is an important tool to help identify blockages, streamline workflows, and optimize resource utilization. This results in reduced delivery times, improved customer satisfaction, and higher productivity.
Lean Production in practice
About the production lines and the warehouse, there are two important highlights in the process SCM Frigo has been implementing. First, each single working station has a specific trolley. For example, “a trolley for the refrigerant component, one for the electrical component, and the other for the mechanical component. They pick the components and they prepare the trolley for each single unit. So, in the end, we have one trolley for each single sub-assembly phase prepared.” The workers have access to the list of components in digital format, eliminating the need for paper. “Next, the warehouse brings the respective trolleys to each working station.”
The second aspect is that each working station has a screen on which it can monitor production status, connected to the central software, as explained before.
In the long run, the main goal is to make the work easier, and more efficient. That’s why SCM Frigo pays attention to where the tools and components are placed: to make sure everything necessary to assemble the unit is close.
The future of CO2 Refrigeration Systems
Looking ahead, the synergy between Lean Production and the CO2 refrigeration sector is promising. As the world focuses more on being green, the demand for eco-friendly cooling solutions is visible. This principle can help meet this demand by making things in a smarter, more innovative way.
Lean Production and CO2 Refrigeration together are moving towards a future where things are made with less waste and more thought for the environment. “From a certain point of view, it is a never-ending story, because in English we call it lean production, but if we use the Japanese name, that it is kaizen. Kaizen means continuous improvement. So the improvement happens every day”.
Keep following us on this journey of innovation and explore other themes and articles in our blog.
Building Connections
On LinkedIn
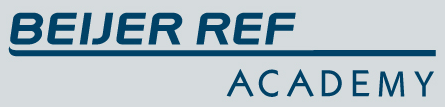
Become a CO² Specialist
Beijer Ref Academy will offer technicians and installers the opportunity to learn how to operate CO2 refrigeration systems in different configurations.