Embracing CO2 Systems in Warm Climates
Embracing CO2 Systems in Warm Climates
Did you know that by 2050, according to the International Energy Agency, global energy demand for air conditioning and refrigeration is expected to triple? We are facing the challenges of a warmer world. So, it’s crucial to understand how innovative technologies like transcritical CO2 refrigeration systems can meet these demands while minimizing environmental impact.
Today, we’ll answer how transcritical CO2 refrigeration systems operate in warm climates and continue “Demystifying CO2 Refrigeration System”. The next step is to dive deeper into the impact of higher ambient temperatures on system efficiency, strategies for overcoming these challenges, the roles of key components, and best practices for maintenance and operation.
Understanding Transcritical CO2 Refrigeration Systems
Transcritical CO2 refrigeration systems are a promising technology to keep things cold without harming the planet. As society and businesses get more worried about the environmental impact of traditional refrigerants, these CO2 systems step in as a smarter, eco-friendly choice. CO2, or carbon dioxide, is the working fluid used in these systems. It is a natural refrigerant with a low global warming potential (GWP) and ozone depletion potential (ODP), making it an attractive choice for businesses and industries that care about the environment.
These systems are also excellent at saving energy, which means companies can lower their operational costs and reduce their carbon footprint at the same time. In a transcritical cycle, CO2 changes from gas to liquid and back again at high pressures. This unique characteristic allows for efficient heat transfer and energy exchange during the cooling process.
The way these CO2 systems work is pretty unique. They use a special cycle that’s different from the traditional vapour compression cycles. Transcritical cycles operate both in the subcritical and supercritical regions of the pressure-temperature diagram.
For businesses looking to be more eco-friendly and save on costs, getting to know how transcritical CO2 systems work is a smart move. This technology is not just good for the planet; it also keeps things cool efficiently.
Challenges in Warm Climates
The primary challenge is the significant increase in ambient temperatures. As temperatures rise, the system must work harder to achieve the desired cooling effect. This leads to increased energy consumption and reduced efficiency.
Pressure and temperature differentials
In transcritical CO2 systems, the critical point of CO2 becomes an important point in warm climates. As temperatures approach or exceed the critical point, maintaining stable pressure and temperature differentials becomes increasingly challenging. This can make the system less reliable and efficient.
Adverse effects on system components
Elevated temperatures can also put additional stress on system components. Compressors, in particular, may experience increased mechanical strain. While heat exchangers and expansion valves may struggle to cope with the heightened thermal demands.
Need for adaptation and optimization
To overcome the challenges posed by warm climates, transcritical CO2 systems require adaptation and optimization. This might mean using smarter ways to control them, making designs that improve heat transfer efficiency, and selecting components that can deal with higher temperatures.
Overcoming the challenges
To keep transcritical CO2 systems running smoothly in warm climates, smart tactics and improvements are essential. Here’s a breakdown of what can be done:
Better system design
The goal is to improve heat transfer efficiency and overall performance. This could mean bigger heat exchangers, better pipe layouts to reduce pressure loss, and integrating secondary loops or subcooling circuits to keep system stability.
Smarter Controls
To keep these systems efficient in the heat, we can use advanced software that predicts the weather and adjusts the system before it gets too warm. Adding sensors and real-time monitoring helps provide real-time feedback and optimization
Better Heat Rejection
Improving how the system rejects excess heat is key, especially with the design and operation of condensers. Making sure this component of the system can deal with high temperatures means the whole system uses less energy and stays more reliable.
Continuous monitoring and maintenance
Regular monitoring and maintenance are crucial. This means watching the system’s vital signs like pressure and temperature and doing routine tasks like cleaning components and fixing leaks to keep the system running smoothly.
Functions of components in warm climates
The key components of transcritical CO2 refrigeration systems work together to ensure efficient and reliable operation, even in the challenges posed by warm climates.
Compressors
Compressors are like the heart of the system, pumping the CO2 around. In warm climates, choosing the right type and size of compressor is super important for keeping things efficient. Variable-speed compressors offer flexibility by adjusting capacity to match changing cooling demands. Scroll or piston compressors are also good choices because they can handle the high pressures that CO2 systems work under.
Heat Exchangers
Heat exchangers are crucial for moving heat in and out of the system, facilitating the refrigeration cycle. In transcritical CO2 systems, evaporators absorb heat from the refrigerated space, while condensers release heat to the atmosphere. To do this well, especially when it’s warm, they need to be designed with enough space for the heat to transfer effectively. Making sure they’re set up right is key to getting rid of unwanted heat efficiently.
Expansion Valves
Expansion valves control how much CO2 flows into the evaporator, which is where the cooling happens. Getting this flow just right is especially tricky in warm weather, but it’s essential for making sure the system works without wasting energy or causing damage. Electronic expansion valves are excellent at this because they can adjust more precisely than traditional mechanical types, keeping the system in control even when temperatures fluctuate.
Gas Coolers
Gas coolers are integral components of refrigeration systems, responsible for dissipating heat from the refrigerant gas and facilitating its transition from a high-pressure, high-temperature state to a lower-pressure, lower-temperature state. By efficiently rejecting heat, gas coolers contribute to the overall performance, reliability, and energy efficiency of the refrigeration systems.
CO2 transcritical gas coolers are designed to efficiently reject heat from CO2 refrigeration systems, particularly in warm climates where ambient temperatures can pose challenges to the cooling process. They are optimized for high-temperature environments through a combination of advanced design features. These include adiabatic pre-cooling, efficient heat exchanger design, optimized airflow management, and sophisticated control systems. This integration ensures that these gas coolers can deliver reliable and efficient performance, even under challenging conditions.
CO2 Refrigeration System types in warm climates
What are the various approaches to CO2 refrigeration in warm climates? Ranging from simple cascade systems to cutting-edge ejector technology, let’s explore them in detail.
Cascade Systems
CO2 has been used in warmer climates mainly in subcritical cascade systems. These systems combine CO2 in the secondary loop with another refrigerant in the primary loop, resulting in high energy efficiency in warm climates. Typically, refrigerants such as HFC (hydrofluorocarbon) or ammonia are used in the primary loop. It’s important to note that the fluid condensing the CO2 and used for refrigeration is generally an HFC (which is discouraged) or ammonia (which is acceptable as it is a natural refrigerant).
However, the use of HFC or ammonia in the primary loop presents certain disadvantages. HFCs have a high global warming potential (GWP), contributing to environmental concerns and regulatory restrictions. Ammonia, while having a low GWP and it is a natural refrigerant, poses safety risks due to its toxicity and flammability, requiring stringent safety measures. Additionally, the initial cost and complexity of cascade systems can make it difficult to adopt CO2 in food retail applications, especially for smaller format stores:
Transcritical Booster Systems
The transcritical booster system is currently the most popular CO2 solution. This system is highly preferred in areas with mild weather. However, in warmer regions, additional technology is needed for energy efficiency that is comparable to or better than non-natural solutions.
Mechanical Sub-Cooling
another method is the mechanical sub-cooling, which made it possible to use transcritical CO2 refrigeration in warmer climates. This method involves connecting a small mechanical vapor-compression cycle to the main cycle at the gas cooler exit to provide sub-cooling. The additional unit only operates when temperatures exceed a certain level, saving energy during peak load times.
Adiabatic gas cooler and water spray systems
Adiabatic gas coolers and water spray systems work together to enhance the performance of CO2 transcritical refrigeration systems in warm climates. The adiabatic process pre-cools the air before it reaches the gas cooler, while the water spray system uses evaporative cooling to further reduce the air temperature. These methods improve the efficiency and reliability of the system, ensuring effective cooling and energy savings even under high ambient temperature conditions.
Parallel Compression
This solution has been developed to use CO2 as the only refrigerant. It focuses on simplification and energy efficiency. It is the first step in making CO2 a viable option in warmer climates, especially for larger installations. This method is gaining popularity as an energy-efficient CO2 solution.
Parallel compression works by compressing the extra gas at the highest pressure level to improve energy efficiency. This approach significantly improves the COP in warm climates.
Ejectors Technology
The understanding of thermodynamics and fluid mechanics has got better over the years. Consequently, so did the performance of ejectors. The conclusion was that they could now reuse more refrigerants and do it better, thus saving energy. The real breakthrough came with smart control systems. Ejectors can now adjust to various situations much more efficiently.
Mirko Bernabei, Technical Director of SCM Frigo, speaks about how “Ejector Technology is one of the technologies that we are trying to push into the market”.
We have explored this theme in more detail here.
According to Danfoss, even though ejector technology is still in the prototype stage, early tests in over 10 supermarkets in developed countries have shown that this technology can improve the efficiency of parallel compression systems. The energy savings are like the improvements seen when initially using parallel compression. Compared to traditional HFC systems, the potential for energy savings is significant. In addition, ejector technology allows for the installation of smaller and more compact compressor packs, reducing the initial installation costs.
Future and Innovations
The future of transcritical CO2 refrigeration systems in warm climates will depend on continued research and development efforts. One thing we are sure: these systems can revolutionize the refrigeration industry, making it greener and more efficient, even in challenging environments. Going forward, transcritical CO2 refrigeration systems are likely to undergo continuous innovation and improvement, with a strong emphasis on efficiency, sustainability, and reliability. This includes advancements in heat exchanger technology, system control, and the integration of energy recovery devices like expanders, all aimed at enhancing performance while minimizing environmental impact.
Building Connections
On LinkedIn
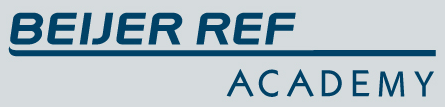
Become a CO² Specialist
Beijer Ref Academy will offer technicians and installers the opportunity to learn how to operate CO2 refrigeration systems in different configurations.